Laser Injection of Soft Faults for the Validation of Dependability
Design
Wilfrido A. Moreno
Center for Microelectronics Research and Electrical Engineering
Department,
College of Engineering, University of South Florida
Moreno@eng.usf.edu
John R. Samson Jr.
Space and Strategic Operations, Honeywell, Inc.
Jrsamson@space.honeywell.com
Fernando J. Falquez
Space and Strategic Operations, Honeywell, Inc.
Falquez@space.honeywell.co
Abstract: The expanding application of computing systems and
the continuing advances in semiconductor technology are forcing the on-chip
inclusion of design for dependability features (concurrent fault tolerance).
These features detect, log and provide recovery from errors induced by
faults concurrently with the operation of the system. A very difficult
task is the hardware validation of concurrent fault tolerant design features
in a nondestructive, unobtrusive manner. A semi-automated facility has
been developed at the University of South Florida for this purpose using
Laser Fault Injection (LFI) to simulate soft errors during system operation.
The facility provides means to extract target coordinates from the CAD
database, synchronize the laser pulse with the operation of and capture
health warnings issued by the system under test. The key fault tolerant
features (automatic instruction retry on single soft errors) of a state
of the art fault tolerant computer for space applications were validated
at this facility.
Key Words: Dependability validation, concurrent fault tolerance,
hardware fault injection, laser fault injection.
1 Introduction
Fault Tolerant Design (FTD) is a discipline that seeks to detect and
resolve conditions that would result in erroneous operation or system failure.
Until recently, and because of its inherent cost, FTD has been implemented
at very high levels in the system hierarchy and only for critical applications.
Examples of these systems include Railway Control Systems [Arlat
et al. 96], the Space Shuttle Control [Marciniak 94],
and air traffic control such as the French Air Traffic Control System [Kanoun
et al. 96]. In general, this means that the system will detect errors
produced by hardware or
software faults to prevent catastrophic results.
The FT approach here is one of full redundancy of computers and software.
Recently, with increased dependence on computerized data, FT has been applied
to distributed and clustered computing and database services to insure
system availability. Examples of these approaches are the Unix based Continuum
400 [Hewlett-Packard webpage 98] and the NT server
based RADIO cluster [Stratus webpage 98]. The approach
here is still one of redundant and replicated modules with special hardware
and software to support FT features such as system reconfiguration.
With the appearance of VLSIC, it has become possible to provide on-chip
circuits to detect, report and recover from errors, concurrently with normal
operation. These features are usually referred to as "on-chip",
"on-line" or "concurrent" FTD. Concurrent FTD has been
applied to high reliability systems that are required to operate in environments
such as outer space [Honeywell 89], [George
95], [Samson 95], where transient faults generated
by high energy particles cause soft errors known as Single Event Upsets
(SEU). However, continuing advances in semiconductor processes are beginning
to have a negative effect on the ability of advanced VLSIC to perform free
of error [Saw et al. 98], [Johnston
et al. 98], [Johnston et al. 97], [Falquez
98]. A figure of merit in [Falquez 98] estimates
that a 0.4 micron system operating at 500 Mhz from a 1.5 V supply is relatively
six orders of magnitude more susceptible to noise or SEU disturbances than
a 4 micron system operating at 1 MHz from a 9 volt supply. An emerging
need for the general application of concurrent FTD is readily apparent.
2 Design Approach to Fault Tolerance
The approach to FTD must be comprehensive and inclusive of all system
aspects from requirements to implementation. A thorough treatment of the
proper approach to FTD is given in [Samson 92]. Characteristically,
FTD is hierarchical, and follows the partitioning and flow-down of requirements
from a very high system level, down to the functional block. The availability,
reliability, and performance requirements of the Global Positioning System
(GPS), for example, ensure that more than three satellites are available
for navigation anywhere in the world, at any time, while exposed to the
environments associated with an earth orbit 20,000 kilometers high. While
satellite availability, reliability and performance requirements are supported
to a great extent by redundancy, the designed characteristics of the electronic
subsystems on board, help to minimize the total number of satellites required
in the constellation. In a similar fashion, the requirements of the functional
blocks flow down from the availability, reliability and performance requirements
of the electronics subsystems. With respect to fault tolerance, the requirement
may be to reconfigure the system after a hard failure, or to recover autonomously
from a soft failure.
2.1 Elements of FTD
The key elements of FTD are the detection, containment and recovery
from fault conditions on components of the system. Three key measures of
the system FT are fault detection latency, fault recovery latency, and
fault coverage.
Detection latency refers to the length of time that a fault condition
goes undetected in the system. Long latency impacts the throughput and
integrity of the system. The cost and impact of the failure to contain
a fault at its originating level increases significantly as erroneous results
are passed on to other parts of the system. Fault detection coverage refers
to the number of faults from a given set the system will detect. Fault
recovery coverage refers to the number of detected faults from which the
system will recover.
2.2 Fault Sets, Fault Models and Error Sets
A fault set establishes the measure applied to the system in order to
determine its fault tolerance. Its derivation is a critical part of the
system requirements definition because it drives the FTD effort. To each
fault or fault type, there corresponds a model of the behavior of the system.
The resulting behavior is described in terms of erroneous results from
which an error set can be derived. The FTD effort then proceeds to identify
the most cost effective means to detect, contain and recover from any of
the errors in the set. A distinction is made between soft errors, which
can be handled by soft recovery, and hard errors, which must be handled
by reconfiguration of the system. The extent to which the system performs
these tasks is a measure of the system FTD.
3 FTD Validation, Related Research and Techniques
A significant challenge facing the design team once the design is done,
is how to validate the design, i.e., show that the concurrent FT requirements
were met. That is, how to inject a transient fault in a specific area of
a system while it is executing a specific function, without introducing
additional embedded hardware or software overhead, and then observe that
the system handled the fault in real time and continued its normal operation.
Validation of FTD has been performed through software means, and at high
levels in the overall system FT hierarchy [Geoghegan
96], [Ayache 96], [Gupta 93],
[Dawson 96], [McIntyre 95], [Benjo
93]. The approach to validation is generally through software injection
of faults at interfaces or protocols, or through the implementation of
self-checking computing systems with checkpoints and rollback. Validation
of concurrent FTD at the microinstruction level can be simulated within
the design environment or with special software tools. Hardware methods
of validation are generally performed at SEU testing facilities. Laser
injection of faults has been used for component threshold determination.
3.1 Simulation-based fault injection
Simulation of faults during the design phase may be required in order
to verify the proper implementation of concurrent fault tolerance. This
can be achieved within design environments such as VERILOG and VHDL. However,
simulation of a complete system including firmware, is very expensive and
time consuming so that time to market requirements and budget constraints
tend to limit this approach to a minimum.
3.2 Fault Injection with Particle beams
High-energy particle beams have been used to determine the Linear Energy
Transfer (LET), and therefore the susceptibility of components to SEU.
However, validation of concurrent fault tolerance at the microinstruction
level at a particle beam facility is limited by the ability to synchronize,
locate and control the beam. Design and implementation of a test to produce
a single soft error at a specific location in the VLSIC, during the execution
of a particular micro-instruction, in order to force a specific fault recovery
mode is a very difficult if possible task. In addition, the test environment
requires precautions for handling a radioactive source, and working through
a vacuum interface.
3.3 Laser Injection of Faults for SEU Threshold Determination
Laser energy deposited in semiconductor material generates free charge
carriers that can upset the Logic State of an operating microcircuit. The
effects of laser induced faults in microcircuits are similar to SEU effects
produced by energetic particles. This similarity has been researched by
a group of scientist [Richter 87], [Buchner
87], [Buchner 88], [Buchner
90], [Gossett 92], [Schneiderwind
92], [Johnston 93], [Buchner
94], [Melinger 94], [Buchner
96], concerned with the correlation of SEU thresholds of bipolar, CMOS,
GaAs technology, memory and logic components. They have sought methods
to correlate upset thresholds found with the laser technique vs. the thresholds
found with ion beams and particle beams [Sexton 96].
They stress the importance of the choice of laser beam wavelength and spot
size with respect to the target material, its doping levels and surface
passivation, when attempting to establish correlation between laser and
ion energy. The absorption characteristics and charge generation processes
are described and compared for the two techniques. The information developed
through the research above can be used as a guide for the choice of laser
and laser parameters when considering Laser Fault Injection (LFI) for FTD
validation.
4 Laser Fault Injection (LFI) for FTD Validation
The objective of LFI testing for FTD validation is to force an error
in the state of a component in an operating FT system and to verify that
the corresponding fault tolerant design features came into play to detect,
record and take the next appropriate action. If the fault is locally recoverable,
operation should resume with the correct present state (automatic instruction
retry). If the fault is not locally recoverable, the fault should be reported
to the next level of the system hierarchy. The design and implementation
of a LFI FTD validation test requires the use of a special laser facility
and the development of a sound methodology to setup and control the test
and observe the results.
4.1 Laser Restructuring Laboratory at USF - CMR
The Laser Restructuring Lab (LRL) facility at the Center for Microelectronics
Research (CMR) of the University of South Florida (USF) was established
in the late 1980?s to investigate Wafer Scale Integration (WSI) restructuring
techniques [Moreno 93]. A diagram of the facility
is shown in Figure 1. The laboratory has a high precision 6 axis (x, y,
z, x-tilt, y-tilt, and x/y planar rotation) translation table with a x/y
positioning accuracy of 0.1 micron. This x y positioning accuracy is attained
using a HP interferometer system. The system was originally built by MIT
Lincoln Laboratory and later moved to USF/CMR to support Wafer Scale Restructuring
research as part of the AMMP (Advanced Microelectronics and Materials Program).
Three lasers can be used with the system table, a Nd:YLF laser, an Argon
laser, and an Excimer laser. The control of the lasers and the translation
table is completely automated. The control station is a 200 MHz Pentium
based PC running a Microsoft Windows 95tm operating environment. Communication
with the table, the z-axis and the laser is through an IEEE 488 bus. Communication
with the tilt and rotation mechanism is through an RS232 channel. Another
RS232 channel is used for communication with the system under test. External
timing and control of the laser is through a digital I/O interface.
The Q-switched Nd:YLF laser is used as the light source in the LFI experiments.
The laser has a fundamental component at 1046 nanometers. A frequency doubler
is used to create laser pulses at a wavelength of 523 nanometers.
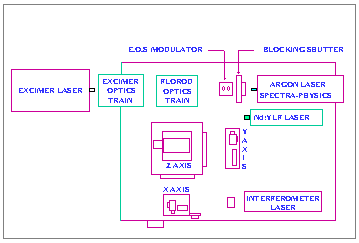
Figure 1. Laser System Layout
The laser is fired manually, or through a synchronization facility.
Figure 2 illustrates the LFI experimental setup. Both mechanical and electrical
control of the Device Under Test (DUT) is necessary to perform the test.
The 0.1-micron positioning accuracy of the laser table is needed to precisely
locate the target area. This is very important for testing the state-of-the-art
chips whose target diffusions may have dimensions on the order of a micron
and which may be obscured by up to three levels of metal.
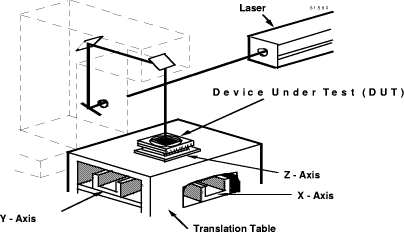
Figure 2. LFI Experiment
The laser beam is directed from the source to the device under test
(DUT) through a series of mirrors and optics as shown. The DUT is mounted
on the translation table. The actual laboratory facility including the
lasers, the optics, and the translation stage used in these experiments
is shown in Figure 3. A video camera mounted on top of the optics tower
passes through the same optics as the laser beam and allows the operator
to see the area being exposed. This facility is convenient, not only for
component registration and alignment, but also to confirm the component
location and the laser injection point with the output of the VLSI design
and layout tools.
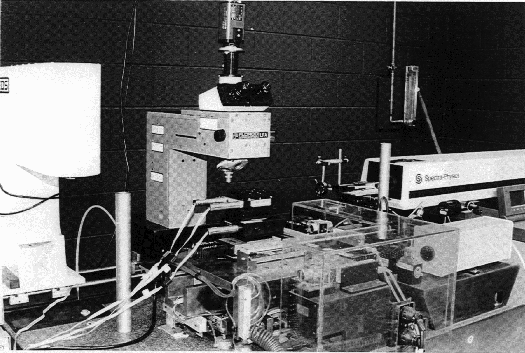
Figure 3. A View of the Laser Restructuring Lab
4.2 LFI Development
The use of Laser Fault Injection for FTD validation was demonstrated
as reported in [Landis 95], [Yoder
94], [Yoder 95], [Moreno 97],
[Samson 97] and [Samson 98].
Samson, Moreno, Landis and Yoder progressed from laser pulse characterization
and manual control, to the demonstration of LFI on components (gates, flip-flops,
ring oscillators and a multiplier), to an initial demonstration of LFI
on a single board space computer. The 10 ns, 523 nanometer green light
output of the Nd:YLF laser was found to produce soft errors at a power
setting of 630 milliwatts without evidence of damage to the DUT after repeated
applications of the pulse. Moreno and Falquez [Falquez
98] developed semi-automated facilities for extraction of target coordinates,
synchronization of the laser pulse with the operation of the FT system
under test and means to capture health warning messages on line with the
test.
5 LFI Test Vehicle
The selected target for the FTD validation test with LFI was an advanced
RISC processor design with on-chip concurrent error detection. This included
Concurrent Error Detection (CED) and fault/error handling logic implemented
as a Single Board Computer (SBC). This design has concurrent error detection
circuitry built into the instruction pipeline, the data pipeline, and the
error-handling pipeline as shown in Figure 4. Parity and EDAC on registers,
multiplexers, and busses, residue checkers on the arithmetic units, and
redundant self-checking on decoders and other logic elements, are examples
of concurrent error detection techniques employed to detect transient and
permanent faults/errors in the design.
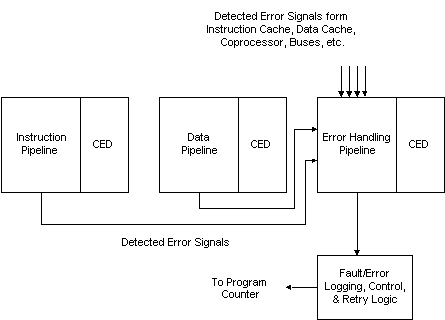
Figure 4. Conceptual View of an Advanced RISC Design
5.1 Automatic Instruction Retry
The key feature of the design implemented by the error handling pipeline
is the ability to complete the micro-instructions that were in progress
prior to the occurrence a recoverable soft error, and to automatically
retry the micro-instruction impacted by the soft error. This is "automatic
instruction retry". It can be appreciated that this process is not
observable unless a message is produced or a history that can be examined
is maintained in special registers in the device.
5.2 Special Registers of the FT SBC
The FT SBC selected for LFI validation tests contains a number of special
registers where health status and history of detected errors and the recovery
action taken is kept. Examination of these registers, or programmed routines
to issue health warnings when an error is handled, allows the observation
of the process. Two such registers are the ERROR COUNTER and the DETAIL
REGISTER.
The ERROR COUNTER register is incremented for every occurrence of an
error- handling event. The DETAIL REGISTER contains a code that describes
the type of error and the functional block affected. The information contained
in these and other special registers such as the INSTRUCTION COUNTER and
embedded SRAMs (REGISTER FILES), can be reported in a HEALTH WARNING issued
by the error handling facility.
5.3 Health Warning Messages
The SBC resident software can be programmed to issue health warnings
from the data stored in the special registers by the error handling facility
during the processing of an error. A sample health warning from the SBC
following the LFI of a single error is given below.
00090BFA
00090BFC
*** A0900 Health Warning
003FF43C: 0091FEC0 <> 00000000
003FF440: 00004EA2 <> 00000000
000000E8: 00004EA2 <> 00000000
000000EC: 0091FEC0 <> 00000000
000000F0: 18181818 <> 00000000
000000F4: 19191919 <> 00000000
000000F8: 0000A438 <> 00000000
000005DC: 00004EA2 <> 00000000
80F20428: 00000001 <> 00000000
00090BFD
00090BFE
00090BFF
The SBC is reporting completion of a test routine by incrementing a
pass count when a recoverable error was handled. The resident software
issued a health warning and reported the present and previous value (all
zeroes) of nine special registers, and then continued with the test routine.
Within the health warning fields, the first column gives the address of
the special register; the second column gives the contents of the register
after the error was handled; the third column gives the previous contents
of the register.
The address of the Detail Register is 000000F8. Its content (0000A438)
indicates that there has been a retryable single error in the register
file. The address of the Error Count Register is 80F20428. Its content
(00000001) indicates that the error count is now 1.
6 LFI Test Procedure
The implementation of the system level LFI test will depend on the set
of tools used for product development and laser control environment. In
the following, references to specific tools can be replaced by the appropriate
equivalent. Prior to the beginning of the tests, a number of preparations
will be required. The specific objective of the test will define the requirements
of the instrumentation and of the test software that the DUT will be executing
during the test. Initialization, synchronization and reporting will also
be a function of the test environment and the test objective. The LFI tests
presented here were aimed at validating the automatic instruction retry
requirements of the FT SBC selected as test vehicle. The procedure steps
were as follows:
- Establish a list of targets and the expected test results. It is important
that simulation data be available for some of the expected results in order
to establish correlation between simulation and test.
- Generate a place and route report. Within the CADENCE GATE ENSEMBLE
tool, this is accomplished by executing the "report placement"
command with the "detail" switch option. This option is necessary
because the component may be placed in a North (N), East (E), South (S),
West (W) orientation. In addition the placement can also be Flipped (F).
Therefore, the placement detail affects the actual location of the particular
area that may be the target within the component.
- Determine the coordinate orientation, origin and scale factor. The
chip x and y coordinate orientation with respect to the laser table must
be determined in order to locate the targets properly, and in order to
mount the DUT such that the table travel-limits do not prevent reaching
the desired location on the chip. In general, the units used by the place
and route tool will not be the same as the units available at the laser
table, so the appropriate scale factor needs to be determined. Also, the
origin of the chip coordinates will not necessarily fall at a corner of
the chip, so the proper offset must be determined.
- Extract the target coordinates from the place and route report. The
place and route report is a very large file because it contains a line
for every physical library component in the design. The Unix filter `grep'
can be used to extract the few lines associated with the target. A sample
extraction for a hypothetical register from a place and route report is
shown in Figure 5. "cpup2" is a place and route report that contains
entries for tens of thousands of components. The extraction is the location
of the 22 bits of the register called RGIDA. The command catalogs the "cpu2"
file, extracts the lines containing RGIDA, sorts on increasing values of
the x coordinate and writes the output to the file called RGIDA. Steps
1 through 4 above can be performed with a single Unix script that
reads
the target list, invokes the place and route tool in a Unix shell in the
background, opens the layout database, generates the report, extracts the
coordinates and writes out a target location file.
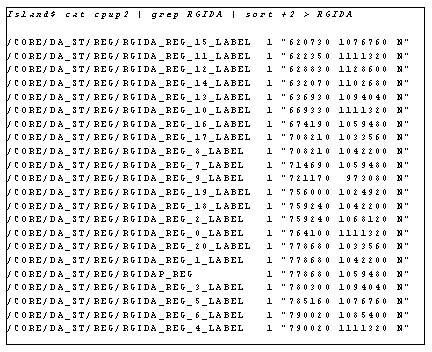
Figure 5. Extraction of Target Coordinates from Place and Route
Report
- Download the target coordinate information to the LFI facility. The
target coordinate file generated above can be easily transferred to the
LFI facility where the proper adjustments for offset and scaling can be
performed. Layout views of the physical components in the design can be
downloaded also to aid in the adjustment for placement orientation. The
coordinate adjustment can be automated through a series of linear transformations
on the reported chip x y location.
- Setup the experiment. Setting up the experiment requires the mounting
of the
- DUT on the x y table and aligning the de-lidded chip to be injected
with laser pulses under the laser beam. Figure 6 shows a diagram of the
LFI test setup.
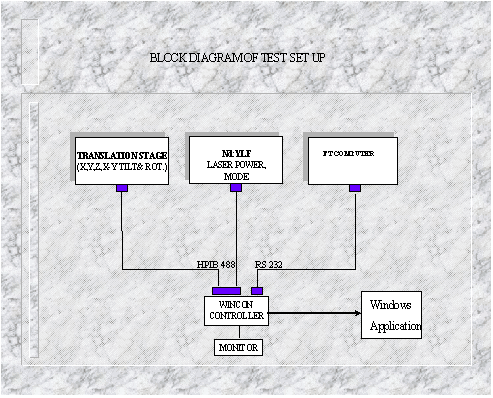
Figure 6. LFI Test Setup
The alignment process is controlled by the Windows application. A functional
check of the DUT executing the LFI test routine should be performed at
this time. The experiment controller can request the DUT through its serial
port, to perform basic memory read, write, clear, reset and run commands.
The controller can also receive responses from the DUT through the same
port. The setup should verify that the DUT can issue discrete outputs,
and that the laser can be triggered with them. Finally, the laser power
should be adjusted and verified using a practice target. The laser pulse
delivered by the Nd:YLF laser head is 10 Ns wide. The power level is controlled
from the Windows application and the level required to produce errors will
vary depending on the clock rate and the semiconductor technology. As the
clock rate increases, the laser power required to produce a soft error
decreases. This effect has been observed and reported [Samson
98a]. For the test sample used and for clock rates of 4 to 6 MHz, a
power setting of 650 down to 625 milliwatts should produce repeatable results.
The laser can be fired asynchronously from the Windows application through
a zap command or through a programmable delay synchronized by a discrete
output form the FT system under test. Another important setup step is to
verify that the facility to capture warning messages in real time is operational.
For the present test, the reset command contains a warning header that
is recognized by this facility. Therefore, when the DUT is reset to start
the test, a
warning message should be recorded. Subsequent messages contain
the status data generated by the soft errors induced by the LFI.
- Load the target coordinates and jog the translation stage to the target.
An inspection of the intended target should be performed in order to verify
that it is not obstructed from view by metallization. The on-line video
camera allows examination of the target area. If required, the beam spot
can be repositioned in 0.1-micron increments. Changes to original target
coordinates should be recorded in the target file. Run the test. To start
the LFI test, reset the DUT and issue the run command. The DUT should respond
with a warning message and with a count of the passes through the test
program. A warning produced by a soft error will interrupt the pass count.
The pass count will be resumed upon completion of the warning. If the laser
is to be fired synchronously, the variable delay trigger to the laser can
be programmed through the Windows application for a single pulse mode.
Once the location is fine-tuned and the laser power is properly adjusted,
production of soft errors at a given target is very repeatable. In the
asynchronous mode, the timing of the pulse with respect to the program
step under execution and with respect to the next clock edge will require
repeated applications of the laser pulse in order to induce an error. The
test program in the DUT continues to run after issuing the warning message.
The pass count is not issued until the end of the pass, therefore, analysis
of the micro-instruction sequence execution immediately following the injected
error is necessary in order to validate the automatic instruction retry
FT feature. This analysis can be performed by examination of the assembly
code listing of the test program and the warning message, which shows the
contents of the Instruction Counter. By following the thread of the listing
from this point, the microinstructions executed to return to the main flow
of the test program can be determined. This analysis was performed for
samples of instruction retry test data. Once this is done, the sequence
of warnings issued by the DUT can be relied on for the validation tests.
7 Automatic Instruction Retry Test Results
LFI tests on a number of bits identified by the procedure just described,
and by inspection of the layout of the register file, were performed to
validate automatic instruction retry features of the FT SBC design. The
tests were repeated numerous times with repeatable results. During the
test sequence, the laser table was dismantled for maintenance and reassembled.
A number of tests were rerun that correlated with initial results. In all
over 500 shots were taken. The computer is still functional. The health
warnings captured agreed 100 percent with the special register contents
predicted by simulation for retryable single soft errors in the data pipeline,
in the instruction pipeline and in the register file. Sample data results
are given below in Figure 7. The figure shows an image of the target, the
x y coordinates of the target, and the captured health warning issued by
the computer after handling the soft error induced by the laser pulse.
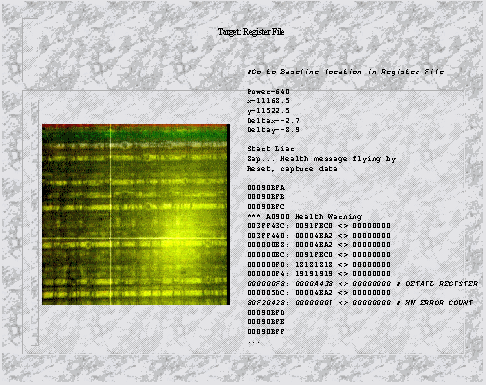
Figure 7. Target: Register File
8 Conclusions
There is an emerging need for the general application of concurrent
FTD in order to preserve the dependability of advanced CMOS VLSIC. A reported
figure of merit indicates that highly scaled CMOS devices are relatively
orders of magnitude more susceptible to soft transient errors than traditional
devices. With this need for the general application of FT systems comes
the need to verify that the error detection and recovery features of the
FT system perform as required. Semi-automated FTD validation methods with
Laser Fault Injection (LFI) have been developed at the University of South
Florida. These methods were applied in the successful testing of automatic
instruction retry features of a state-of-the-art FT single board computer
9 Areas For Future Work
9.1 Fully Automated LFI Test Facility
The LFI test facility provides for semi-automated means to extract target
coordinates, setup the laser, control the test and synchronize laser pulse
with the operation of the DUT. However, some additional automation and
instrumentation enhancements could transform the Laser Laboratory into
a full-up concurrent FTD validation facility.
- 1.Auto alignment. The process of aligning the target can be automated
by means of an expert system trained with layout data from the foundry.
- 2.Auto focusing optics. Auto focusing the laser beam would speed up
the test performance and allow fine tuning the power levels required for
producing soft errors.
- 3.Variable laser frequency. The ability to vary the laser frequency
would allow to quickly re-setup for different semiconductor target materials.
- 4.Physical damage detection. A facility such as an infrared camera
would allow the detection of hot spots and uncover potential damage produced
by the beam. This facility would allow for fine grain characterization
of the power limits to perform LFI on different semiconductor technologies.
- 5.Continuously adjustable optics capable of focusing over a wide range
of magnification powers. This facility would speed up the test set up and
the test performance.
- 6.Automated step and repeat programming. Production testing of FT features
could be automated with this facility. Items 2 and 5 could be integrated
into this capability.
- Instrumentation for high level tests of an operating FT computer network.
This capability could be of significant value to programs such as SBIRS,
GLOBALSTAR, SPACEWAY GPSIIF and other emerging space applications. Operation
of the system could be simulated during a critical period in the presence
of strategically placed and timed soft faults.
9.2 Laser Beam Spot Size
A key issue regarding the continued applicability of LFI to FTD validation
is the need to adapt the laser beam physical characteristics to the changing
semiconductor process parameters. Dense, multi-layer metalization may obscure
the intended targets. Therefore, it is necessary to develop means to shape
the beam to diameters below one micron.
References
[Arlat et al. 96] Arlat J. et al.: "Dependability
of Railway Control Systems". Proc., 26th Int. Symposium on Fault-Tolerant
Computing, Sendai, Japan, 96, 150-155.
[Ayache 96] Ayache S., et. al. :"Formal Methods
For The Validation OF Fault Tolerance In Autonomous Spacecraft", Proc.
Annual International Conference On Fault-Tolerant Computing 96. IEEE, LosAlamitos,
Ca, USA. 96CB35969, 353-357.
[Benjo 93] Benyo B., Pataricza, A., :" Fault
Injection Based Dependability Analysis", Periodica Polytechnica, Electrical
Engineering v 37 n 2 93, 97-101.
[Buchner 87] Buchner S. P., Wilson, D., Kang, K.,
Gill, D., Mazer, J. A., Raburn, W. D., Campbell, A. B., Knudson, A. R.,
:"Laser Simulation Of Single Event Upsets", IEEE Transactions
on Nuclear Science, Vol NS-34, Dec 87.
[Buchner 88] Buchner S., Knudson A., Kang K., Campbell,
A. B., :" Charge Collection from Focused Picosecond Laser Pulses".
IEEE Transactions on Nuclear Science, Vol. 35, No. 6, Dec. 88.
[Buchner 90] Buchner S., Kang K., Stapor W. J.,
Campbell A. B., Knudson A. R., McDonald, P., Rivet, S., :"Pulsed laser
induced SEU in integrated circuits: A method for hardness assurance testing",
IEEE Transactions on Nuclear. Science., NS-37, 90, 1825-1831.
[Buchner 94] Buchner S., Langworthy J. B., Stapor
W. J., Campbell A. B. Rivet S., :"Implications Of The Spatial Dependence
Of The Single-Event-Upset Threshold In SRAMS Measured With A Pulsed Laser".
IEEE Transactions on Nuclear Science, Vol. 41, Dec 94.
[Buchner 96] Buchner S., et. al. :"Modification
of Single Event Upset Cross Section Of An SRAM At High Frequencies",
IEEE Transactions On Nuclear Science, Vol. 43, June 1996.
[Dawson 96] Dawson S., et. al. :"Testing Of
Fault Tolerant and Real-Time Distributed Systems Via Protocol Fault Injection".
Proceedings- Annual International Conference on Fault-Tolerant Computing
96. IEEE, Los Alamitos, Ca. USA, 96CB35969, 404-414.
[Falquez 98] Falquez F. J., :"Fault Tolerance
and Testability Design With Validation by Laser Fault Injection to Improve
the Performance and Testabilty of Advanced VLSIC". Ph.D. Dissertation,
December 98.
[Geoghegan 96] Geoghegan S. J., Avresky, D. :"Design,
Verification, and Validation of Self-checking Software Components";
Proc. International Phoenix Conference on Computers and Communications
96. IEEE, Piscataway, NJ USA, 420-426.
[George 95] George M. D., Brichacek J.: "Radiation
Hardened 32-Bit Processor"; 15th International Communications Satellite
Systems Conference 95.
[Gossett 92] Gossett C. A., Hughlock B. W., Johnston
A. H., :"Laser Simulation Of Single-Particle Effects", IEEE Transactions
On Nuclear Science, Vol. 39, Dec 92.
[Gupta 93] Gupta R., :"Phi-Test: Perfect Hashed
Index Test For Test Response Validation", Proceedings, IEEE International
Conference on Computer Design: VLSI in Computers and Processors 1993. IEEE,
Piscataway, NJ USA. p 588-591
[Hewlett-Packard webpage 98] http://www.hp.com/uk/complementary/stratus1.htm
98.
[Honeywell 89] Honeywell Space and Strategic Avionics
Division,: "Final Technical Report, Contract No. F30602-88-C-0060"
. / October, 89.
[Johnston 93] Johnston A. H., :"Charge Generation
And Collection In p-n Junctions Excited With Pulsed Infrared Lasers",
IEEE Transactions On Nuclear Science, Vol. 40, Dec 93.
[Johnston et al. 97] Johnston A. H., :"Radiation
Effects in Advanced Microelectronics Technologies". Proc. Fourth European
Conference on Radiation and Its Effects on Components and Systems. Sep.
97. Cannes, France. IEEE CN 97 TH 294.
[Johnston et al. 98] Johnston A. H., Swift G. M.,
Shaw D. C. :"Impact of CMOS Scaling on Single-Event Hard Errors in
Space Systems. Jet Propulsion Lab. NASA MSREP Program 98.
[Kanoun et al. 96] Kanoun K., Borrel M., Morteveille
T., Peytavin A.,: "Modeling the Dependability of CAUTRA, a Subset
of the French Air Traffic Control System". Proc. 26th Int. Symposium
on Fault-Tolerant Computing, Sendai, Japan, 96.
[Landis 95] Landis D., Moreno W., et al., :"Enhancing
Fault Coverage of VLSI Circuits: Analysis and Investigation". Unpublished
proposal submitted to Rome Air Development Center. 95.
[Marciniak 94] Marciniak J. J.: "Encyclopedia
of Software Engineering" / John Wiley and Sons 94.
[McIntyre 95] McIntyre M.D. W., Gossett, Cynthia
A. :"BOEING 777 Fault Tolerant Air Data Inertial Reference System,
A New Venture In Working Together", Proc. IEEE/AIAA Digital Avionics
Systems Conference- 95. IEEE, Piwcataway, NJ, USA, 95CB35873, 178-183.
[Melinger 94] Melinger J. S., Buchner S., McMorrow
D., Stapor W. J., Weatherford T. R., Campbell A. B., Eisen H., :"Critical
Evaluation Of The Pulsed Laser Method For Single Event Effects Testing
And Fundamental Studies". IEEE Transactions On Nuclear Science, Vol.
41, Dec 94.
[Moreno 93] Moreno W. A., "Laser Direct Routing
for High Density Interconnects", Ph.D. Dissertation, University of
South Florida, Dec. 93.
[Moreno 97] Moreno W. A., Falquez F. J., Samson
J. R. Jr. :" First Test Results of System Level Fault Tolerant Design
Validation Through Laser Fault Injection". Proc. ICCD97 Conference,
Austin, Tex. Oct. 97, 532-541.
[Richter 87] Richter A. K., and Arimura, I., :"Simulation
of heavy charged particle tracks using focused laser beams", IEEE
Transactions on Nuclear Science, NS-34, 87, 1234-123910.
[Samson 92] Samson J. R. Jr., :"Optimizing
Real-Time Fault Tolerance Design in VLSI and Wafer Scale Architectures
for Real-Time Parallel Processing". Ph. D. Dissertation, University
of South Florida, May 92.
[Samson 95] Samson J. R. Jr., "What Is So Special
About the RH32?" Honeywell Engineering Pulse, 95.
[Samson 97] Samson J. R. Jr., Moreno W. A., Falquez
F. J." Validating Fault Tolerant Designs Using Laser Fault Injection
(LFI). Proceedings, DFT97, Paris, France. Oct 97.
[Samson 98] Samson J. R. Jr., Moreno W. A., Falquez
F. J. "A Technique For Automated Validation Of Fault Tolerant Designs
Using Laser Fault Injection (LFI)" Proceedings, IEEE Symposium on
Fault Tolerant Computing. Munich, Germany. June 98.
[Samson 98a] Samson J. R. Jr., "Technology
Seminar-Frequency Dependent SEU in Logic Circuits. Trip Report", Honeywell
Internal Correspondence. October 1998.
[Saw et al. 98] Saw D. C., Swift M., Johnston A.
H.,: "Space Radiation Effects on Low Power Advanced-Technology. 1)
Rams." Jet Propulsion Laboratory. NASA MSREP Program 98.
[Schneiderwind 92] Schneiderwind R., Krening D.,
Buchner S. Kang K., Weatherford T. R.,:" Laser Confirmation Of SEU
Experiments In GaAs MESFET Combinational Logic", IEEE Transactions
On Nuclear Science, Vol. 39, Dec 92.
[Sexton 96] Sexton F. W., "Microbeam Studies
of Single-Event Effects," IEEE Transactions on Nuclear Science, Vol.
43 No. 2, 96, 687-695.
[Stratus webpage] http://www.gsk.net/profile/products/description/stratus/radio/radio.html
98.
[Yoder 94] Yoder J. and Landis D., :"The Testing
of Fault Tolerant Circuits Using Lasers", Proc. of GOMAC Conference,
Nov. 94.
[Yoder 95] Yoder J. W., :"Transient Fault Tolerance
In 2D Message Passing Networks For ULSI", Ph.D. Dissertation, University
of South Florida, Aug. 95.
|