A Modular Architecture for Nodes in Wireless Sensor Networks
Jorge Portilla
(Universidad Politécnica de Madrid, Spain
jportilla@etsii.upm.es)
Angel de Castro
(Universidad Politécnica de Madrid, Spain
adcastro@etsii.upm.es)
Eduardo de la Torre
(Universidad Politécnica de Madrid, Spain
eduardo.delatorre@upm.es)
Teresa Riesgo
(Universidad Politécnica de Madrid, Spain
teresa.riesgo@upm.es)
Abstract: The growth of sensor networks during the last years
is a fact and within this field, wireless sensor networks are growing particularly
as there are many applications that demand the use of many nodes, even
hundreds or thousands. More and more applications are emerging to solve
several problems in data acquisition and control in different environments,
taking advantage of this technology. In this context, hardware design of
the sensor network node becomes critical to satisfy the hard constraints
imposed by wireless sensor networks, like low power consumption, low size
and low cost. Moreover, these nodes must be capable of sensing, processing
and communicating physical parameters, becoming true smart sensors in a
network. With this goal in mind, we propose a modular architecture for
the nodes, composed of four layers: communication, processing, power supply
and sensing. The purpose is to minimize the redesign effort as well as
to make the node flexible and adaptable to many different applications.
In a first prototype of the node, we present a node with a mixed design
based on a microcontroller and an FPGA for the processing layer and Bluetooth
technology for communications.
Keywords: Wireless sensor networks, modular architecture, sensor
network node, hardware node design
Categories: B.5.1, B.6.0, B.7.0
1 Introduction
Measurement and control of all kind of parameters in several application
scenarios raises some problems and design challenges for researchers. Wireless
sensor networks appear as a solution, where hundreds or thousands of sensor
nodes take measurements from the environment, process the information and
communicate this data to the network and to the final user [Zhang,
04]. This field has grown enormously during the last years and it is
expected that this trend continues in the future [Hill,
00] [Chong, 03].
These networks are composed of nodes with several constraints due to
the nature of the wireless sensor network field, like very low power consumption
or very low cost and reliability of the nodes. With sensor networks it
is possible to improve the measurement procedure since human intervention
is reduced almost totally.
Usually, developers focused on a centralized architecture for the system
(see Figure 1) where the central node acts as the master
and the sensors/actuators as slaves. The master takes information from
the slaves, processes it and acts consequently. This approach presents
several drawbacks like bottlenecks in the central node and high dependence
on the reliability of the master.
On the other hand, a distributed architecture arises as another approach
(Figure 1) [de Castro, 02],
in which each node processes locally the signals from sensors, and communicates
them to the network. In this context, if a node fails the network continues
working. Furthermore, the traffic of information is reduced, because each
node can take decisions locally.
Figure 1: Centralized architecture and distributed architecture
of sensor networks
As it has been said before, the wireless sensor networks field imposes
several constraints to the researchers. Because of this, hardware design
of the network nodes becomes critical. This is the point in which this
paper is focused.
Normally, each application fixes its requirements, and the engineers
have to design the system from scratch. This makes redesigning hard and
expensive both in terms of time and cost. To solve this problem it is possible
to divide the node in functional blocks or layers and so, the redesign
effort concentrates in each layer separately. With this approach, it is
possible to reuse layers and interchange between different solutions depending
on the application requirements.
Keeping this idea in mind, a modular architecture of four layers
is proposed for the wireless sensor network nodes (Figure
2). These four layers are: communication, processing, power supply
and sensing/actuation. Each layer fulfils a specific functionality in the
node, and the layers can change between different applications and moreover,
it is possible to have an heterogeneous network with nodes composed of
different layers. Layers are bonded through vertical connectors which are
common to all the layers. As all the layers use the same connectors in
the same position, reusability and interchangeability are much easier.
Figure 2 Four layers node architecture and physical aspect
of the node
2 State of the art of nodes used in wireless sensor
networks
Several groups work in different hardware platforms for the node in
wireless sensor networks, with different conceptions and similarities as
well. In the following sections some remarkable work groups' approaches
will be described briefly.
2.1 U.C. Berkeley Mica® motes
The Mica mote is an embedded platform composed of an Atmega128 microcontroller
from Atmel, a radio module TR1000 from Zeevo and two AA batteries. Moreover,
the system has an expansion connector that allows adding different sensor
PCBs. The platform runs TinyOS, an operating system created in U.C. in
Berkeley as well. TinyOS is an event based operating system in which individual
components act together to form a complete application and to implement
all system functions [Hill, 02]. There are different
Mica models, including versions with ZigBee technology (MicaZ). These motes
are commercialized through a company called Crossbow [Crosbow,
05].
Modularity is achieved through a vertical connector allowing the addition
of sensor boards to the mote. The connector is a 51-pin vertical connector
that allows the addition of different sensor boards depending of the parameters
to be measured. In this way, modularity is understood as a two layers architecture,
where communication, power supply and processing are fixed, representing
one layer. Flexibility is intended for the second layer, which includes
the sensors.
2.2 Intel® iMote®
The Intel Mote platform includes Bluetooth communications and an ARM
core, both in the same chip, a TC200IP from Zeevo. The software architecture
is based in the porting of TinyOS to the ARM core [Nachman,
05]. They integrate vertical stackable connectors, in order to make
the platform customizable and flexible. In the future, they want to have
the sensor board and the power board together in the same system with the
main board [Intel, 05], but up to now, they only have
one layer (the main board with processing and communications).
The connectors expose two UARTs, USB, general I/O ports and power, in
order to facilitate research. In this way custom sensor boards and debug
boards can be attached to the iMote® in a straightforward manner.
2.3 MIT Media Lab modular platform
They have developed a modular platform in which each specific board
represents a specific sensing modality (inertial sensing, ambient sensing,
etc.). These sensor boards or panes have data collection as their main
function [Benbasat, 05]. Their platform is modular
as well, with vertical connectors to allow easy combination and recombination
of the different panes when the application changes. The purpose is to
make a platform as modular as possible, making a general system instead
of a specific one. Modularity is applied to the software too, with the
intention of have software blocks specific for each pane.
The platform includes a master pane, a power regulation pane, a storage
pane and different sensing panes depending on the applications. In this
way the number of panes is not rigid, and several different panes can be
developed depending on the different measures to be taken. The architecture,
therefore, implies two fixed layers (master and power regulation) and different
possibilities to be added depending on the application.
The electrical connections make different signals and power available
for the panes. The connectors are two vertical headers of 14 and 12 pins,
which are not very robust.
2.4 Tyndall Institute
Tyndall Institute developed a platform for wireless sensor networks,
stackable and modular. The platform runs an adapted version of TinyOS.
On the other hand, the platform can include an FPGA module, for fast DSP
processing. They have some sensor layers for different applications and
the power supply layer can include batteries or energy harvesting elements.
The system incorporates a 2.4 GHz transceiver with a special protocol to
minimize power consumption [O'Flynn, 05]. Moreover,
they have developed an 802.15.4 compliant layer for communication, in order
to have a standard technology in this field.
Layers can be interchanged in an easy way, thanks to the vertical connectors,
and include communication, processing, sensing and power supply. So they
exhibit a four layers design similar to the design presented in this article.
3 Four layers architecture
In this section, the modularity concept and the four layers of the architecture
will be detailed.
3.1 Modularity
Modularity is an important feature of the node. The purpose is
to have a modular platform, flexible and adaptable to several applications
and scenarios, and to be able to reuse and interchange between different
layers when the application changes. Moreover, the architecture must satisfy
several design requirements as it has been said before. To achieve this
goal, a four layers modular architecture is proposed.
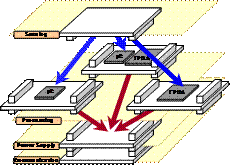
Figure 3: Illustration of modularity
With a modular platform new advantages arise, like easy redesigning
or the possibility of reusing and interchanging layers (see Figure
3), which reduces cost and time. Furthermore, with this architecture
new research possibilities can be tested easily due to the versatility
and flexibility of the system. In fact, the node is intended for both research
and as a demonstrator of new applications.
The modularity is achieved thanks to the vertical connectors. These
connectors fulfil the electrical and mechanical connection, and moreover,
the logic connection, that is, the connections between the different devices
of the architecture (µC, FPGA, sensors, etc.). The connections are
fixed in order to standardize the physical architecture of the node. So,
it is possible to interchange between different layers, and design new
layers in an easy way. Finally, the result is that to interchange between
different layers (two sensing layers for example) the only thing to be
done is to take out the old layer from the node, take the new layer and
insert it in the node, using the vertical connectors.
The use of vertical connectors is useful not only to make the mechanical
and electrical connections, but to reduce node size, taking advantage of
the vertical dimension. This is a trend followed by the different groups
in the bibliography, as it was seen in section 2. All
these factors make the node very robust and compact.
The signals are distributed following some conventions. Assuming that
the µC is in the left side and the FPGA is in the right side, the
connectors will be called left and right connector. In this way, analog
and simple digital sensor signals are connected to left connector pins,
as they can be connected directly to the µC. On the other hand, complex
digital signals are bonded to the right connector in order to be connected
to the FPGA that can easily handle several signals or protocols at the
same time thanks to its concurrency (all the logic is executed simultaneously).
Moreover, supply and ground signals have been placed in the corners of
the connector, as can be seen in Figure 4.
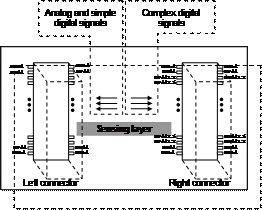
Figure 4: Distribution of signals and connectors
An example of modularity can be seen in Figure 5.
There, two different processing layers are shown, one of them with a µC
and an FPGA and the other one only with a µC. The first example is
a processing layer which should be used in applications which need fast
processing or with sensors with complex digital interfaces. The µC
deals with simple analog signals and with communications, and the FPGA
releases the µC from the tasks related to complex sensors, for example.
The second example should be used in applications with analog sensors (the
µC has an integrated ADC), or perhaps simple digital sensors, where
the µC can face all the work without problems.
Figure 5: Two different processing layers for different application
requirements
3.2 Processing layer
This module provides the smart sensor with intelligence. Here, the signals
from the sensors are converted into appropriate digital and processed signals.
Moreover, the control of the communications is carried out in this module.
Searching of neighbour nodes, setting and breaking links, and management
of all the tasks related with the network are controlled here by generating
commands to the Bluetooth module, and interpreting commands from the Bluetooth
module and other network nodes.
Power saving modes are managed here too in order to extend the battery
life. This is an important matter in wireless sensor networks because it
is required that the network works autonomously for a long time without
human intervention.
A mixed microcontroller/FPGA design is proposed in the first implementation
in order to satisfy different requirements for several applications. Versatility
is the aim of this election, existing other possibilities such as using
the microcontroller only, or the FPGA only.
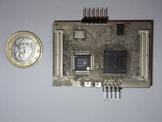
Figure 6: Processing layer hardware
3.2.1 The µC
The µC is an ADUC812 from Analog Devices. This device incorporates
8KB flash memory, 256 bytes of RAM, ADC, DAC, UART and SPI ports, four
general I/O ports, and three timers among others peripherals.
The µC manages the communications, controlling the Bluetooth module
directly through its UART port, and controls the signals from analog and
simple digital sensors as well. The clock frecuency in the first prototype
is 12 MHz, extendable to 16 MHz.
3.2.2 The FPGA
The FPGA is a Spartan III from Xilinx, specifically an XC3S200 (which
integrates 200k logic gates). This device gives the node a big freedom
to adapt to new applications, and makes the system versatile in its processing
capabilities.
The main feature of FPGAs is concurrency. This allows the processing
layer to manage complex digital sensors in a fast way, releasing the µC
of these tasks. In this context, the µC deals with communication
and simple sensors, and the FPGA processes the most complex signals.
The FPGA needs three different power voltages, specifically 3.3, 2.5
and 1.2 V. These voltages come from the power supply layer; this point
will be commented later on.
3.3 Sensing layer
This module includes sensors and/or actuators to interact with the environment.
According to the use of the smart sensor network, multiple combinations
are possible. Multiple kinds of sensors can be included in this level,
and actuators may be incorporated as well in order to act according to
parameters measured from the environment.
In a first application, two different sensor layers have been designed
and manufactured. The former is composed of analog and digital sensors,
and the latter only includes digital sensors (see Figure
7). This is the first demonstration of modularity in the nodes.
The digital version for sensor layer includes an accelerometer and three
different temperature sensors. In this way, there are four different signal
formats to be processed in the FPGA in order to explore the different interfaces
characteristics. In the analog and digital version of sensor layer, sensors
of temperature, humidity, infrared and illumination are included. This
layer is controlled using both the µC and the FPGA. On the other
hand, communications are always managed by the µC.
Figure 7: Two sensing layers, with digital sensors and with
analog and digital sensors
3.4 Communication layer
In the communication layer a Bluetooth module has been chosen for the
first prototype (see Figure 8). This election was done
because Bluetooth has low power consumption, enough data rate for the intended
applications, it is a widely used technology and works in the 2.4 GHz ISM
free license frecuency band.
The module incorporated to the node is a OEMSPA13i from ConnectBlue.
This module acts as a serial cable replacement. The µC communicates
with the Bluetooth module through its UART port. In this way, the module
receives simple AT commands from the µC, commands which make the
module perform different tasks like search for other modules, establish
or break connections, or commands to configure the module, for example.
In order to achieve modularity, several communication layers will be
considered. With the purpose of deal with the possible interfaces of each
wireless module, the µC integrates different interfaces like UART,
SPI, and general I/O ports.
Anyway, the FPGA can solve any problem related to interfacing with the
communications layer because it is possible to virtually implement any
circuit inside this device. Vertical connectors make this possible, because
many signals pass through the communication layer to the processing layer.
This point has been taken into account specially to ensure compatibility
of the node with future versions of the different layers.
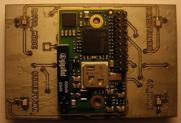
Figure 8: Communication layer with the Bluetooth module
Other technologies are being studied in order to adapt the module to
other application scenarios and to reduce power consumption and network
complexity, like ZigBee or a proprietary protocol.
3.5 Power supply layer
This layer generates all the voltages that are needed by the different
devices of the node. In the first prototype, the layer takes 5V from an
external power supply. With linear regulators the layer supplies 3.3, 2.5
and 1.2 V to the node. These voltages supply the different devices of the
node (the FPGA needs the three voltages to work). Inside this layer (see
Figure 9) there are the largest capacitors of the node
(10 µF), in order to satisfy peak current demands coming from the
processing layer.
Because of the purpose of having autonomous nodes, different options
are being studied in order to integrate new sources like coin cells or
AA batteries. In that case, power consumption must be reduced as much as
possible.
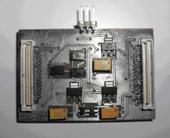
Figure 9: Power supply layer
4 Applications
The number of applications which can take advantage of wireless sensor
networks is huge. This modular solution copes with many different requirements
in terms of performance and cost. This technology allows taking measurements
from the environment in a way very different from that available up to
know. Among these multiple applications we have:
- Home automation and domotics.
- Health systems.
- Structural monitoring.
- Traffic control.
- Military applications.
- Agriculture.
- Elderly people surveillance.
With wireless sensor networks, a new dimension in data acquisition and
control arises. A myriad of sensors take measurements from the environment,
sometimes in inaccessible places, and process the information, taking decisions
if necessary. Human intervention is practically eliminated, and the procedure
of measurement improves, although in this aspect node reliability is an
important topic.
With all these applications fields, it is natural that the sensor networks
research area has grown so much during the last years, with several groups
researching many topics related to this discipline (communication protocols,
power consumption reduction, hardware node design, software, etc.).
Inside these different applications, the first framework in which this
work focuses is domotics. The measurement and control of parameters in
buildings and homes, in order to make life easier and save energy is a
strong trend in R & D today. In the future, homes will be full of sensor
network nodes, in a non intrusive way, watching everything that happens
in the surrounding area. This network will communicate with the PC, a PDA,
a mobile telephone or even electrical appliances.
Depending on the requirements of the building or home, different implementations
of the node can be used. It is possible to have presence detectors, light,
temperature, humidity, pressure sensors, actuators to take part in environmental
conditions, etc. A set of modules available will be chosen to compose the
node. Moreover, if new requirements are imposed, redesign is easy, centering
in one layer and more likely in software. This makes the platform very
useful and versatile and the reduction of cost is notable.
Independently of this first approach, the node is designed to be used
in many different applications scenarios, like industries, forests, roads
or parkings. The possibilities are unlimited, and modularity helps to adapt
the node to all these different situations. Future developments of the
prototype will show the benefits and features of the design.
5 Conclusions
The increasing importance of sensor networks and, particularly, wireless
sensor networks arises new challenges to engineers in several fields. In
this context, hardware node design is critical, in order to satisfy hard
requirements imposed by the wireless sensor networks field, like power
consumption and reduced size.
Usually, a change in the application implies redesigning from scratch
all the system, which drives to high cost and time inefficiency. So, an
ideal solution would be to have a platform that is versatile and adaptable
to new situations with minimum redesign effort. A modular architecture
for the network node is proposed, in order to achieve these objectives.
The architecture is made up of four layers or modules. These layers
are communication, processing, power supply and sensing/actuating. A set
of these layers is available to create the node for a specific application
scenario. Changing of application implies changing the layers or redesigning
one or some of them, but in a very easy way.
6 Future Work
This platform offers a very good opportunity to investigate different
aspects of sensor networks. Different cases of study are being considered
for future implementations of the node.
- Communication layer: different technologies are being studied
in order to have different options for communications. ZigBee is a good
candidate because of its lower power consumption, the easiness to create
networks of a lot of nodes and the recent technology expansion. A proprietary
protocol is another option.
- Power supply layer: New sources must be integrated in order
to make the node autonomous, like coin cells, batteries, energy harvesting
sources or Power Paper [Power Paper, 05].
- Processing layer: other designs must be implemented in order
to face different requirements of new applications. New µC and low
power FPGAs are being studied.
- Sensing layer: new sensors and actuators in new sensor layers
must be developed and produced to cover different scenarios and situations.
References
[Benbasat, 05] A.Y. Benbasat, J.A. Paradiso, A compact
modular wireless sensor platform, Fourth International Symposium on Information
Processing in Sensor Networks (IPSN05), pp. 410 - 415, April 2005.
[Chong, 03] Chee-Yee Chong, S.P. Kumar, Sensor
networks: evolution, opportunities, and challenges, in Proceedings of the
IEEE, pp. 1247 - 1256, August 2003.
[Crosbow, 05] www.xbow.com
[de Castro, 02] A. de Castro, J.M. Chaquet, E.Morejon,
T. Riesgo, J. Uceda, A System-on-Chip for Smart Sensors, in Proceedings
of the 2002 IEEE International Symposium on Industrial Electronics, vol.2,
pp. 595-599, November 2002.
[Hill, 00] J. Hill, R. Szewcyk, A. Woo, D. Culler,
S. Hollar, K. Pister, System Architecture Directions for Networked Sensors,
in Proceedings of the ninth international conference on Architectural support
for programming languages and operating systems (ASPLOS00), vol. 34, Issue
5, December 2000, 93-104.
[Hill, 02] J. Hill, D. Culler, Mica: a Wireless
Platform for Deeply Embedded Networks, in IEEE Micro, vol. 22, Issue 6,
pp. 12-24, November-December 2002.
[Intel, 05] Intel: Intel Research, Sensor Nets/RFID:
Intel Mote, http://www.intel.com/research/exploratory/motes.htm
[Nachman, 05] L. Nachman, R. Kling, R. Adler, J.
Huang, V. Hummel, The Intel Mote Platform: a Bluetooth-based Sensor Network
for Industrial Monitoring, in Fourth International Symposium on Information
Processing in Sensor Networks (IPSN05), pp. 437- 442, April 2005.
[O'Flynn, 05] B. O'Flynn, S. Bellis, K. Delaney,
J. Barton, S.C. O'Mathuna, AM. Barroso, J. Benson, U. Roedig, C. Sreenan,
The Development of a Novel Minaturized Modular Platform for Wireless Sensor
Networks, in Fourth International Symposium on Information Processing in
Sensor Networks (IPSN05), pp. 370 - 375, April 2005.
[Power Paper, 05] http://www.powerpaper.com/
[Zhang, 04] Yong Zhang, Yikang Gu, V. Vlatkovic,
Xiaojuan Wang, Progress of Smart Sensors and Smart Sensor Networks, in
Proceedings of World Congress on Intelligent Control and Automation, vol.4,
pp. 3600-3606, June 2004.
|